Organizations with a large amount of machinery understand the need for maintenance management. It is necessary to ensure that the assets work consistently, do not break down unexpectedly, live longer, and cost less. While many firms have automated the majority of their processes, equipment maintenance management is still done using antiquated technologies such as pen and paper or excel spreadsheets. Fortunately, organizations today are implementing maintenance work order software. These firms benefit from work order software by having streamlined maintenance management, simplified repairs, reduced downtime, and increased asset reliability.
However, not all maintenance management systems are cost-efficient, effective, or simple to use; you must select one that meets your requirements from a market with hundreds, if not thousands, of CMMS programs.
Without further ado, let’s get into work order software, its key features, and how CloudApper CMMS is perfect for the majority of organizations.
Maintenance work order software in a nutshell
Work order software, CMMS software, work order app, maintenance management system, and other terms are used interchangeably. Whatever term you use, they all serve the same purpose.
Work order software aids in the management of maintenance work orders, emergency maintenance requests, spare parts and inventories, technician movement, and the standard description – work order management software entails much more. It collects and analyzes maintenance data to provide important insights that maintenance managers can use to make better maintenance decisions, spot problematic assets, identify critical work orders, enhance efficiency, and so on.
Because it is so similar to CMMS software, the phrases are used interchangeably, and we will do so in this post as well.
Maintenance work order software is perhaps one of the most useful tools in the maintenance team’s armory. When used appropriately, an excellent one assists maintenance teams:
- Simplify their daily tasks
- Keep track of all work orders
- Organize maintenance management information
- Quickly retrieve asset information
- Provide feedback and updates
Work order management software reduces unexpected equipment breakdowns, improves asset reliability, reduces many costs, minimizes workplace safety events, and boosts productivity for the organization.
One of the most useful aspects of maintenance work order software is its ability to help schedule normal maintenance tasks. For example, if a lathe machine needs to be cleaned every two days, the work order software may schedule the task, generate a recurring work order, assign the technician, and add the necessary tools. While the maintenance technician can label the task as “finished” and offer updates if any abnormalities are discovered, the supervisor can check the task’s progress, which keeps everyone informed. That is only one example, but organizing all maintenance tasks with work order software would enhance efficiency, allow for better tracking, increase coordination, and ensure accountability.
A modern CMMS software solution, such as CloudApper CMMS, also allows for mobility; it can be accessible by a number of smartphones, tablets, and PCs, guaranteeing that the maintenance team can do all of the above and more while on the go.
The essential features of a maintenance work order solution
A work order management system includes several features; a competent one includes the following:
- Work order request management
- Work order management
- Asset management
- Parts and inventory management
- Vendor managementÂ
- Technician managementÂ
- PM task scheduling
While the features listed above are basic, competent CMMS solutions, such as CloudApper CMMS, include an analytics dashboard, report generating, email and push notifications, photo and video uploads, QR/barcode scanning, mobile version, and much more. The best part is that CloudApper CMMS can be highly customized to meet your particular requirements, making it an important choice for most organizations.
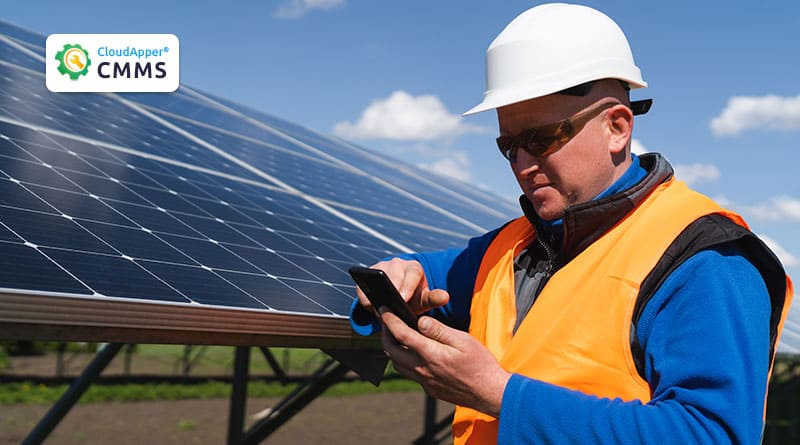
While those are the elements of a maintenance work order system, let’s take a closer look at how most organizations use them.
How do you use a work order system?
While maintenance management is a massive and never-ending task, a maintenance work order process makes it possible, but this is easier said than done. Let’s look at it from the standpoint of a maintenance team that is utilizing CloudApper CMMS for the first time and how they may use it for future maintenance tasks.
Maintenance managers integrate all maintenance management information in the CMMS application, such as assets, work history, spare parts, inventory, vendor, maintenance team, and so on. Later, they schedule routine maintenance tasks, create work orders, assign specialists, specify extra parts or components needed, and provide any other information.
On the technicians’ end, they receive notifications on their smartphones about the allocated work orders and all of the information. After completing the work order, the technicians use their phones or tablets to update the status. If any of the equipment has problems, technicians take photos/videos of the scenario and store them for future inspections.
Anyone in an organization can typically report for emergency maintenance. For example, suppose a conveyor belt fails to function properly. In that case, the machine operator can utilize CloudApper CMMS to report the problem and attach a photo or video to provide a clearer picture. The emergency request is received on the app by the maintenance manager, who examines the case and assigns a technician to inspect and repair the equipment. When the technician arrives at the asset’s location, they can scan the QR/barcode (if attached to the equipment) to immediately access all the information rather than ruffling through excel sheets, reducing response times. When the problem is diagnosed, and all of the necessary materials for repairs are available, the maintenance technician works to repair the conveyor belt and return it to service. As can be seen, CloudApper CMMS substantially simplifies repairs.
CloudApper CMMS can also handle spare parts, ensuring that an adequate supply is always accessible for important equipment. The analytics dashboard also gives useful information for maintenance managers to identify best-performing assets, problematic assets, open work requests, important work orders, and more. Maintenance managers can configure the dashboard to offer the information they need to understand better what’s going on at their plants or facilities.
Contact us now to explore how our solution can improve work order management.
What is CloudApper AI Platform?
CloudApper AI is an advanced platform that enables organizations to integrate AI into their existing enterprise systems effortlessly, without the need for technical expertise, costly development, or upgrading the underlying infrastructure. By transforming legacy systems into AI-capable solutions, CloudApper allows companies to harness the power of Generative AI quickly and efficiently. This approach has been successfully implemented with leading systems like UKG, Workday, Oracle, Paradox, Amazon AWS Bedrock and can be applied across various industries, helping businesses enhance productivity, automate processes, and gain deeper insights without the usual complexities. With CloudApper AI, you can start experiencing the transformative benefits of AI today. Learn More