Table of Contents
Heavy equipment is an important element of companies such as construction companies, farming companies, and mining enterprises. Their activities are largely reliant on heavy machinery, and even if one of the machines fails, it will cause ongoing projects to be delayed. Furthermore, the various pieces of heavy equipment are complex, necessitate large investments, and are exorbitantly expensive to replace. As a result, organizations place a high priority on maintaining this equipment. Unfortunately, not all organizations can provide adequate maintenance management, resulting in unexpected breakdowns, emergency maintenance, and even premature replacements. While that summarized the significance of heavy equipment maintenance management, let’s take a closer look at which assets come into the category and how to optimize them for your machinery.
Common heavy equipment used by various organizations
Heavy equipment normally refers to all machinery designed for specific, difficult operations. As previously said, many organizations employ various types of heavy equipment, some of which are as follows:
- Construction equipment – boom lifts, forklifts, bulldozers, excavators, asphalt pavers.
- Earthmoving machinery – bulldozers, backhoes, loaders, motor graders, trenchers.
- Agricultural machinery – harvesters, tractors.
Some heavy equipment is utilized by multiple industries, while others are exclusively suitable for a specific one. Whatever the case, they are both expensive and essential for everyday operations, making heavy equipment maintenance management necessary for asset reliability and optimum performance.
Optimizing heavy equipment maintenance management with three strategies
Implement SOPs/checklists
Checklists and SOPs (standard operating procedures) are two of the most powerful tools for improving heavy equipment maintenance management. It enables technicians to complete work orders precisely and without variations. Most maintenance procedures must be completed in a specific order, and if a technician deviates from this, it may take longer, waste resources, or be useless. Furthermore, without checklists or SOPs, the maintenance technician may forget a step or two since they can’t recall all the activities because they have so many responsibilities.
As a result, using SOPs and checklists can assist minimize the time it takes to complete repair orders, enhance productivity, and ensure that they are done flawlessly, hence improving asset reliability and ensuring optimal performance.
Provide the option for operators to give feedbackÂ
Incorporating feedback from the person in charge of the machinery – the machine operators – is one of the best methods to improve heavy equipment maintenance management at your facilities. They know the ins and outs of the machinery, how it works when components need to be replaced, and so on. Furthermore, they are aware of any issues that may arise with the machine.
As a result, providing a platform for machine operators to provide feedback on the machines can aid in the detection of difficulties in real-time. Maintenance teams may learn about leaks, breaks, degradation, and other issues and work on them, dramatically lowering response times and unexpected downtime.
Machine operators and workers can use their smartphones to report malfunctioning equipment and request emergency maintenance by informing the maintenance staff. The maintenance manager may then assess the problem, issue a work order, and assign a technician to repair the machine, streamlining and digitizing the entire process. CloudApper CMMS, our CMMS software, can assist with this. Furthermore, our solution is highly customizable by users (built with a no-code platform) and can be accessed via smartphones, tablets, and PCs. It includes a marketplace with access to a plethora of mobile enterprise applications.
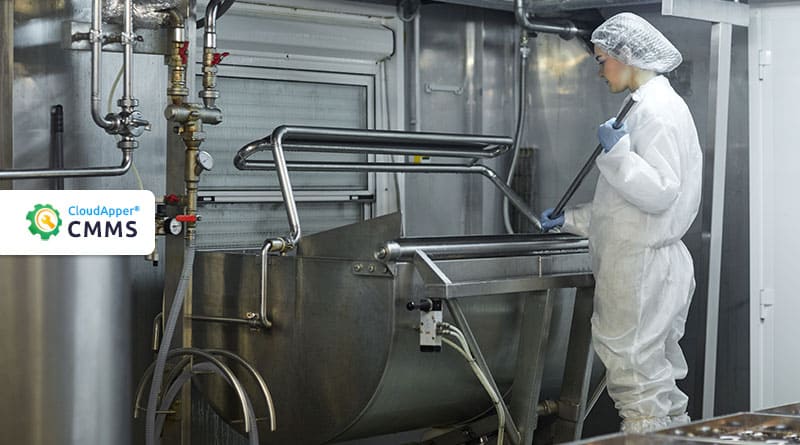
Speed up maintenance tasks with dedicated tools
Like SOPs, there are specialized, standard tools required for various tasks, which are referred to as service packs. An inspection, for example, necessitates (but is not limited to) a CMMS solution, a device to use it with, tools for carrying it out, a wrench, protective equipment, and so on. While the technician is using the CMMS on their smartphone or tablet, the other tools must be ready ahead of time to avoid delays. Technicians can prepare service packs a day ahead of time to ensure that the tools are ready, preventing complications at the last minute and identifying any concerns ahead of time.
CloudApper CMMS helps streamline heavy equipment maintenance
Using smartphones and tablets, CloudApper CMMS simplifies preventive maintenance for your heavy equipment. It ensures asset management, spare parts and inventory management, work order and request management, vendor management, and more while centralizing all maintenance information. Users may readily access the information no matter where they are, ensuring on-the-go maintenance and repairs!
Contact us now about CloudApper CMMS to see how it simplifies heavy machinery maintenance, reduces downtime, and improves performance.
What is CloudApper AI Platform?
CloudApper AI is an advanced platform that enables organizations to integrate AI into their existing enterprise systems effortlessly, without the need for technical expertise, costly development, or upgrading the underlying infrastructure. By transforming legacy systems into AI-capable solutions, CloudApper allows companies to harness the power of Generative AI quickly and efficiently. This approach has been successfully implemented with leading systems like UKG, Workday, Oracle, Paradox, Amazon AWS Bedrock and can be applied across various industries, helping businesses enhance productivity, automate processes, and gain deeper insights without the usual complexities. With CloudApper AI, you can start experiencing the transformative benefits of AI today. Learn More