Table of Contents
Machine maintenance has always been important to organizations requiring expensive and complex pieces of equipment to operate, such as those within the construction, manufacturing, and mining industries, to name a few. However, even smaller organizations nowadays use critical systems and equipment that require maintenance. For instance, HVAC systems, generators, sprinklers, and alarm systems are relatively common. Whenever these crucial pieces of equipment are unable to function properly, they not only cause disruptions to the processes they’re used for, but other processes will often also feel their effects. Losses, workplace safety incidents, higher costs, and higher unplanned downtime are just some of the impacts that organizations experience down the line. As a result, equipment maintenance is crucial at all times.
As such, today, we’ll be doing a deep analysis of five tips and tricks that can optimize equipment maintenance within your facility and improve equipment reliability in the process.Â
Five tips and tricks to optimize machine maintenance
Create a planned backlog
While preventive maintenance usually focuses on scheduled maintenance, it also acknowledges emergency (or unexpected) maintenance requests. However, responsible maintenance managers should know that they likely cannot process or approve every emergency maintenance request that comes in. As such, there are several factors managers need to consider, such as resource restraints, ongoing maintenance activities, budget constraints, spare parts availability, or the asset’s priority.
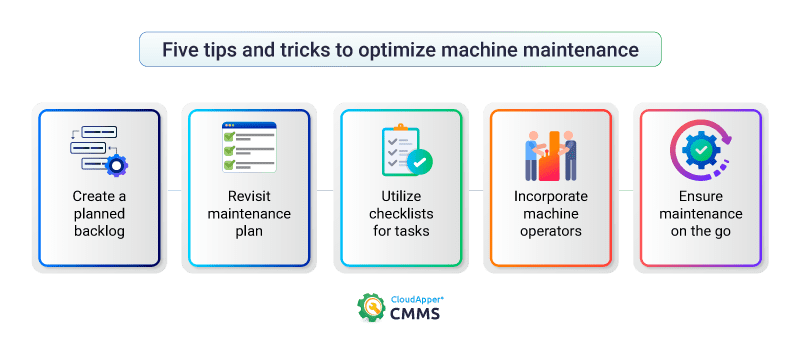
However, responsible maintenance managers won’t necessarily reject these emergency maintenance tasks, but they should keep them in the maintenance backlog. Nevertheless, they recognize that the business’s technicians will need to conduct these emergency repairs down the line, or else they could lead to more significant problems such as workplace safety issues, breakdowns, overheating, etc. As a result, keeping, maintaining, and working on the maintenance backlog helps organizations deal with deferred emergency maintenance tasks effectively and in due time.
Revisit the maintenance plan
Do you already have a maintenance plan with scheduled maintenance activities, and yet still experience significant asset reliability issues? Are assets continuing to cause problems even after receiving maintenance?
Chances are, you might need to take a second look at your maintenance plan.
Ensure an effective preventive maintenance plan is in place for the various machinery types within your facility. A frequent mistake that organizations make is that they bombard their equipment with over-maintenance. To prevent this issue, you should identify the procedures that other businesses with the same machinery are implementing, look at the equipment’s manual, or conduct research for online forums about the machine and its faults. However, this is just one aspect of the maintenance plan – you should always inspect the other elements to identify whether they need changes or not. Doing so helps save considerable costs down the line and optimizes machine maintenance effectiveness.Â
Utilize a checklist for crucial tasks
Maintenance technicians have countless tasks on their hands at any one time; they’re always working on inspecting, servicing, or replacing spare parts of equipment. And, since they’re only human, it’s quite understandable that they might forget a step or two when they’re executing assigned work orders.
Utilizing checklists can hence help technicians execute tasks properly and ensure that nothing is missed. Generating a checklist for each maintenance work order might seem time-consuming, but it ensures that the task is performed accurately by completing all the required steps. Utilizing lists for crucial work orders and maintenance tasks optimizes machine maintenance, reduces unexpected equipment breakdown, and increases business productivity overall.Â
Build a relationship with the machine operators
Modern maintenance managers know that simply executing machine maintenance tasks isn’t enough for effective maintenance; they also need to consider other factors, such as the machine operators. Since machine operators are the ones who closely work with the equipment, they have a great level of insight into how the machine works, what problems they face, when the device needs lubrication, cleaning, etc.
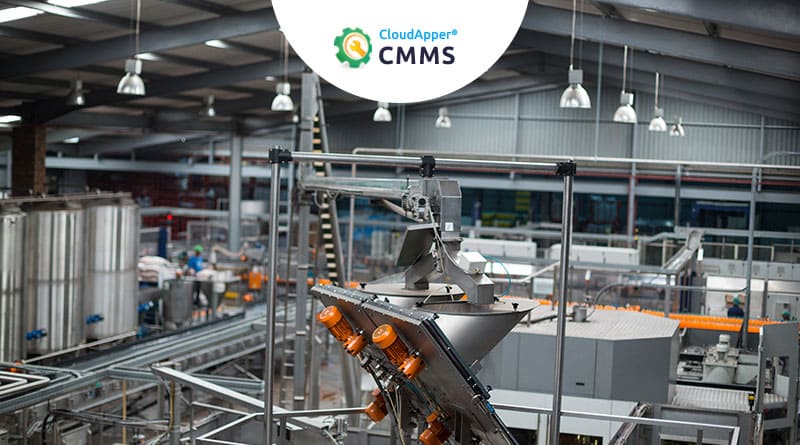
Thus, building and fostering a healthy relationship with the machine operators can help maintenance managers obtain firsthand knowledge about the equipment. Also, incorporating the feedback from machine operators can further optimize machine maintenance. For instance, as we have already mentioned, the maintenance team can learn exactly when lubrication or cleaning might be necessary; moreover, they can determine which challenges represent the most problematic aspects of the equipment.
Ensure preventive maintenance on the go
Preventive maintenance is one of the most balanced approaches that organizations can use to improve asset reliability. However, even though the assets are scattered across the facilities, floors, and plants, maintenance technicians must execute work orders, inspections, and repairs effectively, efficiently, and on the go.
A robust CMMS software solution such as CloudApper CMMS can help with this requirement.Â
CloudApper CMMS helps with preventive maintenance, simplifies repairs, and ensures that work orders are completed on the go. Authorized personnel can use the app from their smartphones and tablets. The tool provides maintenance schedule management, vendor management, asset management, spare parts management, and more. Meanwhile, users can modify all of these systems themselves since the tool is built with a no-code enterprise app development platform known as CloudApper.
Imagine that your organization could implement a solution that you’ve built according to your unique maintenance requirements – the possibilities are endless – contact us now to learn more!
What is CloudApper AI Platform?
CloudApper AI is an advanced platform that enables organizations to integrate AI into their existing enterprise systems effortlessly, without the need for technical expertise, costly development, or upgrading the underlying infrastructure. By transforming legacy systems into AI-capable solutions, CloudApper allows companies to harness the power of Generative AI quickly and efficiently. This approach has been successfully implemented with leading systems like UKG, Workday, Oracle, Paradox, Amazon AWS Bedrock and can be applied across various industries, helping businesses enhance productivity, automate processes, and gain deeper insights without the usual complexities. With CloudApper AI, you can start experiencing the transformative benefits of AI today. Learn More