Table of Contents
While maintenance management has been around for a long time by now, the only option for years was reactive maintenance, which simply isn’t an effective strategy anymore. It focuses only on repairs and provides these after the equipment malfunctions. On the other hand, modern maintenance management approaches, such as preventive maintenance, focus on improving asset reliability, reducing unplanned downtime, and extending the asset’s lifespan. All of this helps minimize emergency maintenance, repair, and replacement costs. However, an effective computerized maintenance management system can even help reduce costs further.
With that being said, let’s see how a CMMS solution helps minimize various costs.Â
Five ways a maintenance management system reduces costs
By minimizing unplanned breakdowns and downtime
Fixing equipment after it breaks down is potentially costly. That’s because equipment problems can come out of the blue, disrupting operations and adding to unplanned downtime. With reactive maintenance, there’s a high chance that the parts and tools needed aren’t at hand, and getting them as soon as possible can be costly due to factors such as express delivery – if this is possible at all. Indeed, if the parts and tools aren’t available, the operations will be delayed until the machine can be fixed, incurring further costs down the line.
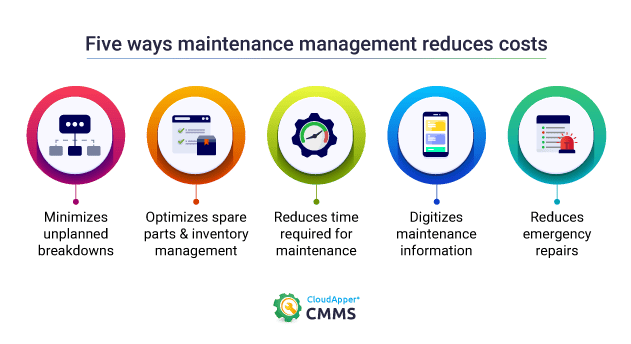
On the other hand, preventive maintenance and a robust maintenance management system can help machinery and equipment receive maintenance and inspections as needed to run reliably and efficiently. By planning and scheduling maintenance activities and assigning technicians appropriately, maintenance managers ensure that all business equipment is cleaned, lubricated, and inspected regularly. All of these activities help reduce unexpected equipment malfunctions, breakdowns, and unplanned downtime and cut all of the costs associated with them.Â
By optimizing spare parts and inventory management
An effective modern maintenance management system, such as CloudApper CMMS, has many valuable features, including inventory and parts management. With such a solution, maintenance managers can easily optimize the inventory level needed for the maintenance of equipment. Accordingly, the maintenance team can identify which parts need to be purchased, which already exist, and the number required. Moreover, the maintenance technicians can also report if ample spare parts are available or not, helping keep everyone on the same page.
By optimizing spare parts and inventory, maintenance managers ensure that the required tools are available at the right time and ensure that maintenance activities are completed within expected deadlines, thereby reducing costs, downtime, and disruptions.Â
By reducing the time required for maintenance
With a modern CMMS software solution, maintenance managers can help optimize maintenance tasks and reduce the time required to execute them. Planning and scheduling tasks beforehand help control several aspects more effectively, such as which spare parts are needed, which technician should complete the work order, the anticipated duration of the job, etc. Moreover, for routine maintenance tasks, technician(s) can easily follow existing instructions attached to the work order, sticking to standardized procedures that help them become efficient and finish the tasks timely.
On the other hand, reactive maintenance focuses only on repairs and doesn’t include a focus on maintenance tasks such as lubrication and inspections. This means that there will be more emergency maintenance tasks involved with reactive maintenance, which are unplanned, more time-consuming, and more expensive for the organization.
By digitizing maintenance management information
Digitizing maintenance information might be one of the most underrated benefits of maintenance management systems; let’s dive in with an example.
Without a CMMS solution, all work orders, inventory technicians, and equipment details are often held in spreadsheets, binders, and recorded paper. Indeed, maintenance management information can be overwhelming to implement and utilize using traditional methods, even with effectively designed spreadsheets. For instance, retrieving the work history of a particular piece of equipment can be a time-consuming and difficult process in its own right, especially if the organization has several machines and uses outdated methods for recordkeeping.Â
A maintenance management solution such as CloudApper CMMS, on the other hand, digitizes all of the information and keeps it organized in a central location. Users can easily access the data just by using their smartphones – yes, it’s that easy!Â
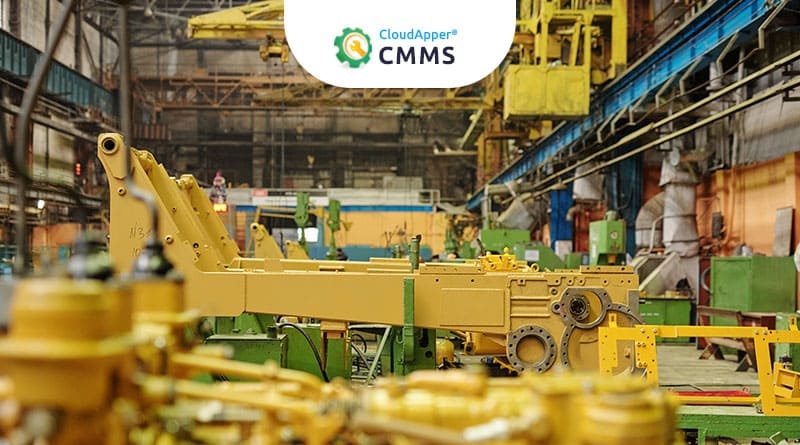
For instance, regular workers such as machine operators can use the app to request emergency maintenance. When the maintenance manager receives the work request, instead of going through hundreds of binders or paperwork, they can easily view the work history of the equipment directly from the app, making it convenient and saving a lot of time. Moreover, technicians can scan barcodes on the equipment to retrieve all the asset’s relevant information, further saving time. These are some examples of how digitizing maintenance information can save time, improve efficiency, and hence reduce costs.
By reducing emergency repairs
Reactive maintenance, as mentioned above, is all about carrying out emergency repairs. More regular repairs mean that the asset will be getting fixed rather than undergoing maintenance. As such, it’s likely to overheat again and perform poorly until it breaks down again, leading to permanent damage as well as faster wear and tear.Â
While preventive maintenance also influences emergency maintenance, compared to reactive approaches, they are much fewer and farther between. With preventative maintenance, the equipment receives all the necessary maintenance in a timely manner, such as inspections, lubrication management, parts replacement, etc., leading to fewer breakdowns, better performance, and fewer emergency repairs being required.Â
CloudApper CMMS is the ideal maintenance management system
CloudApper CMMS is a highly customizable CMMS software solution that comes with all the necessary features, from asset management, technician management, and maintenance scheduling through to inventory management and a powerful analytics dashboard. What’s more, authorized users can customize the system to perfectly fit their organization’s needs. The best part is that it can be used directly from your smartphone device, making maintenance management mobile and more accessible than ever – contact us now to learn more.Â
What is CloudApper AI Platform?
CloudApper AI is an advanced platform that enables organizations to integrate AI into their existing enterprise systems effortlessly, without the need for technical expertise, costly development, or upgrading the underlying infrastructure. By transforming legacy systems into AI-capable solutions, CloudApper allows companies to harness the power of Generative AI quickly and efficiently. This approach has been successfully implemented with leading systems like UKG, Workday, Oracle, Paradox, Amazon AWS Bedrock and can be applied across various industries, helping businesses enhance productivity, automate processes, and gain deeper insights without the usual complexities. With CloudApper AI, you can start experiencing the transformative benefits of AI today. Learn More