Manufacturers using Workday can avoid costly hardware markups by switching to CloudApper hrPad, a tablet-based TimeClock solution. This alternative offers flexibility, scalability, and seamless integration, eliminating the need for traditional, expensive TimeClock hardware.
Table of Contents
Workday users in manufacturing face unique challenges when it comes to workforce compliance—especially around accurate time tracking, clock-ins, and audit-readiness. In high-regulation environments, even small errors in timekeeping can lead to penalties, wage disputes, or failed audits. Unfortunately, many Workday users in manufacturing struggle with delays caused by forgotten passwords, missed punches, or manual entry errors that create gaps in compliance. These seemingly minor issues can snowball into serious risks if not addressed proactively.
For more information on CloudApper hrPad visit our page here.
With Chinese TimeClock prices up 150%, manufacturers relying on physical clock-in devices are feeling the pressure. From inflated import costs to long shipping delays and ongoing maintenance expenses, the cost of time tracking infrastructure is reaching unsustainable levels. This becomes even more complicated for organizations using Workday, where the need for real-time, integrated tracking is essential.
To explore practical alternatives, we gathered insights from professionals involved in HR systems, workforce management, and plant operations. The recurring theme? Workday users can avoid hardware markups by switching to CloudApper hrPad—a tablet-based TimeClock solution built for flexibility, scalability, and direct Workday integration.
What Industry Professionals Are Saying
“Every plant expansion brings the same problem—how to scale TimeClocks quickly without blowing the budget. Hardware quotes are getting ridiculous, especially with tariffs and freight costs. We needed a way to cut deployment time and eliminate markup-heavy equipment.”
“Some facilities are still waiting months for imported clocks. Meanwhile, tablets are sitting idle in storage. Switching to hrPad turned those devices into fully functional TimeClocks in a matter of hours. No shipping, no hardware dependencies.”
“Time tracking accuracy is non-negotiable in manufacturing. But traditional TimeClocks require ongoing maintenance. With hrPad, there’s no physical hardware to fail. The software updates itself, and everything connects to Workday instantly.”
“In high-volume operations, even a few minutes of downtime matters. With physical clocks, one failure can disrupt an entire shift. Tablet-based clocks reduce that risk—and offer flexibility we didn’t have before.”
The takeaway? Relying on expensive, rigid hardware is becoming increasingly difficult to justify—especially when software-based alternatives like hrPad are readily available and already compatible with Workday.
Why CloudApper hrPad Is a Fit for Manufacturing Environments
Manufacturing organizations need tools that are fast to deploy, easy to maintain, and able to scale across multiple sites. CloudApper hrPad meets these requirements with:
- Workday time tracking without physical time clocks
- Instant setup on Android or iOS tablets already in use on the shop floor
- Real-time integration with Workday payroll and scheduling workflows
- Support for digital attestations and timecard confirmations
- No shipping delays, installation wait times, or hardware maintenance needs
This makes it an ideal fit for manufacturers with tight production schedules, lean teams, and multi-location operations. Plus, it ensures compliance without the overhead that hardware-based systems typically introduce.
And most importantly—it directly helps Workday users avoid hardware markups, especially as global hardware prices continue to rise.
Expert Consensus: Drop the Hardware, Keep the Accuracy
Across the industry, professionals are arriving at the same conclusion: hardware-dependent time tracking is outdated and unsustainable. Manufacturers who continue to rely on physical TimeClocks are now contending with:
- Extended hardware lead times due to supply chain issues
- Increased import tariffs and shipping costs
- High upfront investments and maintenance contracts
- Limited flexibility when expanding to new locations or shifts
By shifting to CloudApper hrPad, manufacturers gain a TimeClock solution that works right out of the box—no shipping delays, no physical device requirements, and no complicated installations.
Here’s what organizations gain from making the switch:
- Lower deployment costs across multiple facilities
- Reduced reliance on physical infrastructure and IT teams
- A more agile time-tracking process that scales effortlessly
- Deployment of new locations in hours, not weeks
Final Thought
For manufacturers using Workday, the shift away from traditional TimeClocks isn’t just a modernization move—it’s a strategic necessity. With increasing costs, longer deployment times, and more complex hardware dependencies, legacy TimeClocks no longer align with the needs of today’s agile manufacturing operations.
CloudApper hrPad provides the flexibility, cost control, and seamless Workday integration that manufacturing teams demand—without the baggage of traditional hardware.
What is CloudApper AI Platform?
CloudApper AI is an advanced platform that enables organizations to integrate AI into their existing enterprise systems effortlessly, without the need for technical expertise, costly development, or upgrading the underlying infrastructure. By transforming legacy systems into AI-capable solutions, CloudApper allows companies to harness the power of Generative AI quickly and efficiently. This approach has been successfully implemented with leading systems like UKG, Workday, Oracle, Paradox, Amazon AWS Bedrock and can be applied across various industries, helping businesses enhance productivity, automate processes, and gain deeper insights without the usual complexities. With CloudApper AI, you can start experiencing the transformative benefits of AI today. Learn More
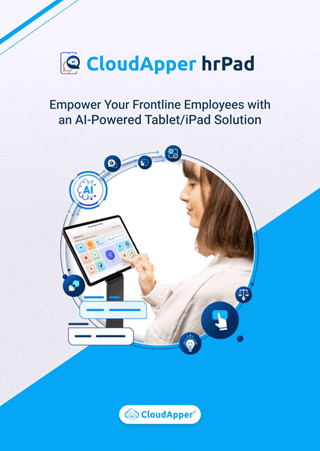
Brochure
CloudApper hrPad
Empower Frontline Employees with an AI-Powered Tablet/iPad Solution
Download Brochure
CloudApper AI Solutions for HR
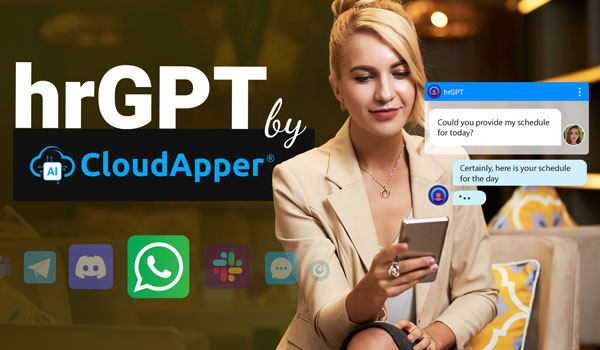
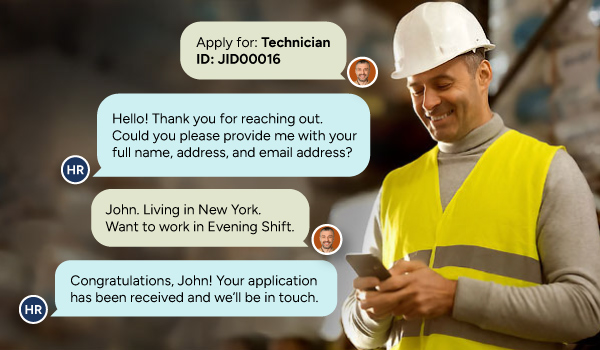
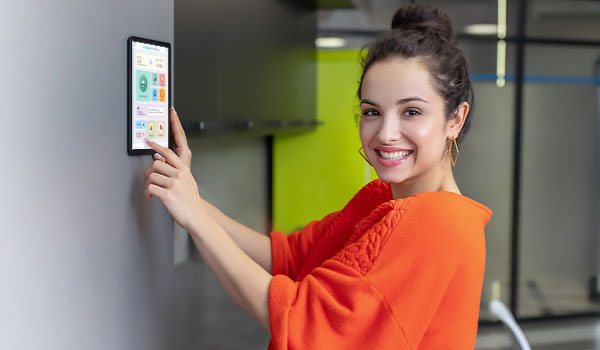
- Works with
- and more.
Similar Posts
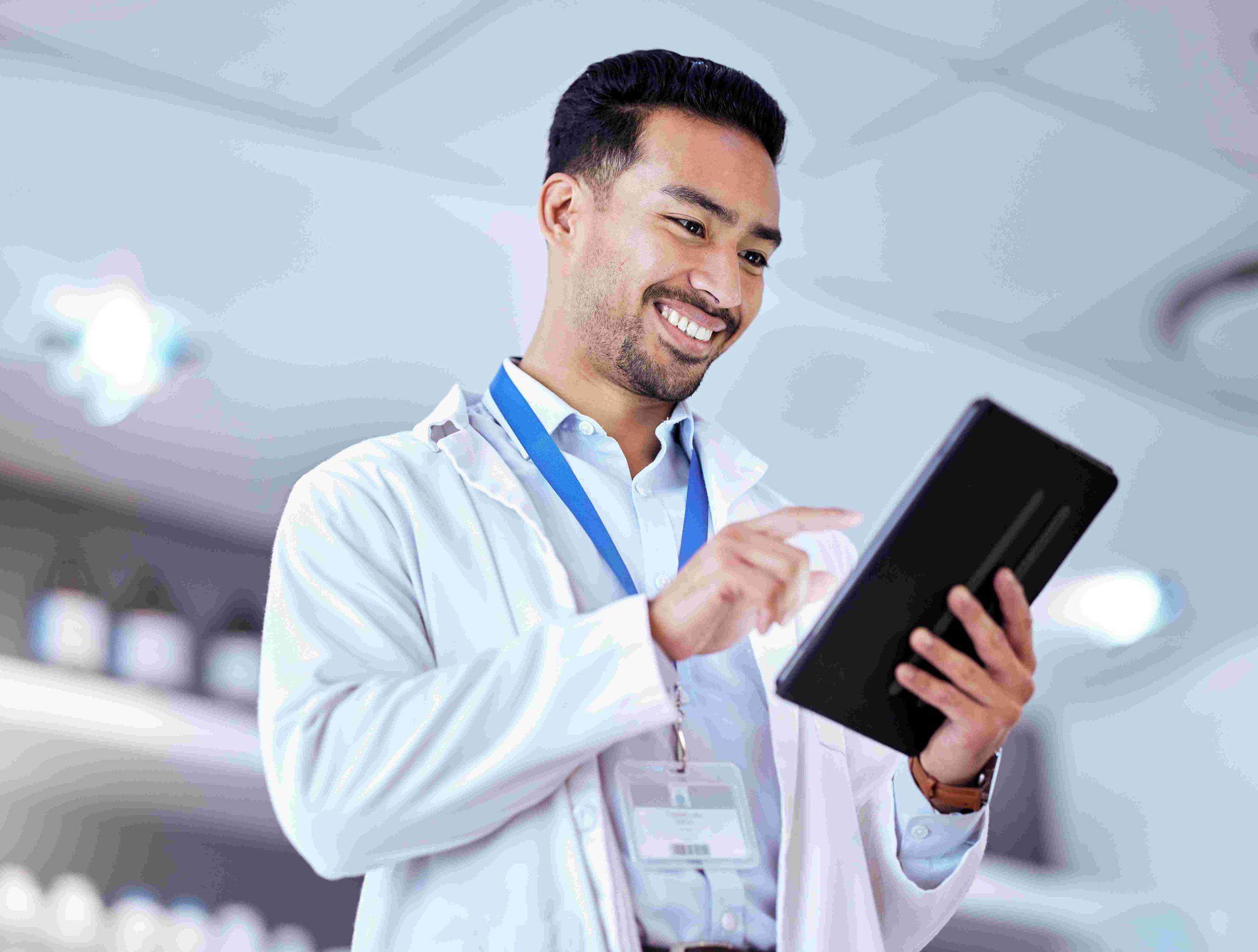
Why It’s Time for Healthcare Organizations Using Workday to Rethink…
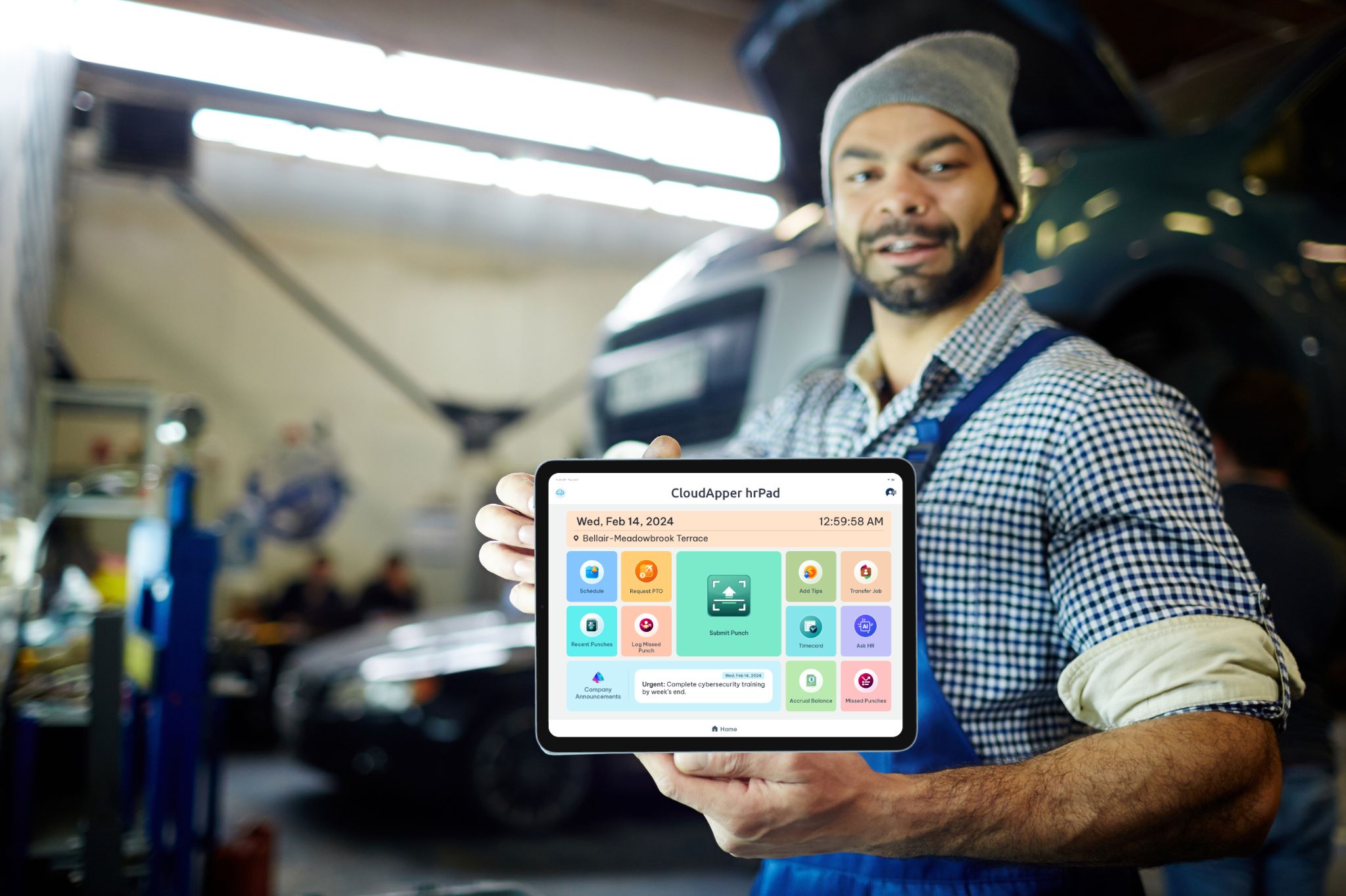
Switch to Tablets: Here’s How Workday Users Can Avoid Hardware…
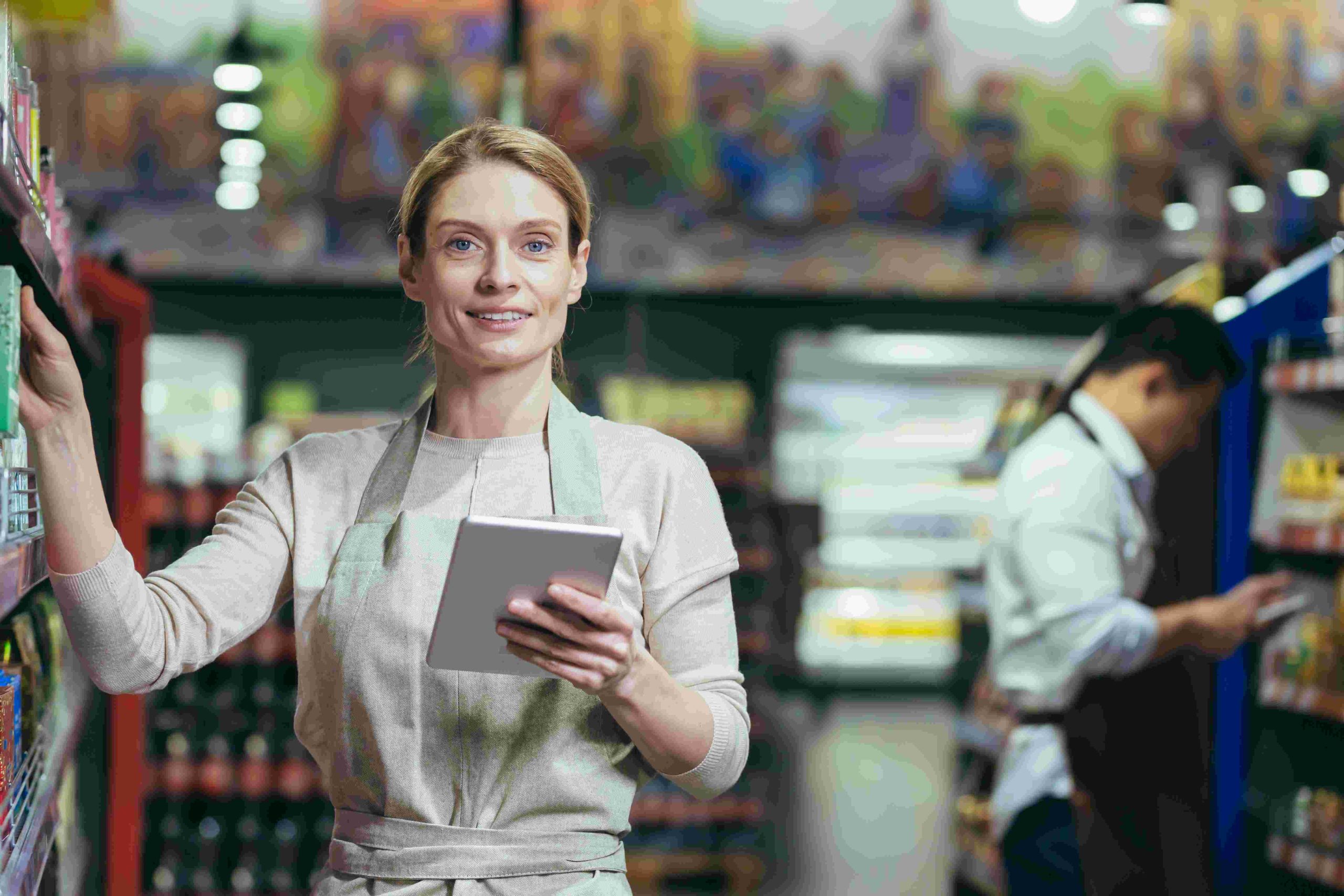